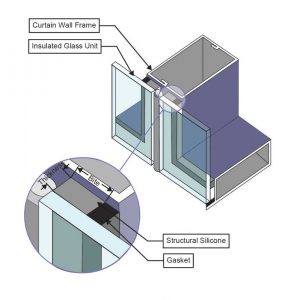
Field-installed structural sealant glazing (SSG)
The term SSG refers to the use of structural sealant to secure façade components, most commonly IGUs but also metal panels and other glazing materials, onto a façade system such as a curtain wall frame. SSG can function as both part of the structural load path for the glazed element and part of the air-and-water barrier for the façade system.
IGUs secured with SSG are commonly either two-sided (i.e. partially captured) or four-sided (i.e. the SSG is the sole structural attachment). The continuity of SSG in four-sided systems offers enhanced air-and-water infiltration resistance compared with two-sided systems, which often use interior gaskets on the captured sides; however, assuming no supplemental pressure caps, four-sided systems rely solely on the SSG for structural support and attachment of the glazed element and are of greatest concern for quality-related failures.
This article will refer to SSG as it relates to field glazing or reglazing of IGUs into an aluminum curtain wall frame, but most considerations are also applicable for glass spandrel lites, metal panels, and other glazing materials in similar façade systems. A typical shop-fabricated curtain wall with four-sided SSG is depicted in Figure 1.
1. Field-installed SSG failures
The failure of SSG can be any deviation from specified airtightness, watertightness, or structural performance criteria of the SSG assembly. Poor quality installations of SSG can result in failures such as air infiltration/exfiltration, condensation issues, water intrusion, biological growth, and in some cases catastrophic structural failure and loss of attachment of the glazed components.
Failures of field installed SSG often occur because of workmanship related sealant problems due to improper or inadequate installation procedures and poor surface preparation and/or access to install sealant, or general or weather constraints. Workmanship related failures typically include the presence of bubbles and voids in the sealant as well as insufficient sealant bite width, adhesion, cure, or joint discontinuities (Figure 2, page 52).
In the authors’ experience, the structural sealant material itself is typically not a source of failure if stored properly and used for the intended application before the product expiration date, but careful sealant selection for the intended application is a critical factor for success.
Other problems can occur due to inconsistent quality control measures, poor project management, or simply installer mistakes. Some examples include use of an incompatible or inappropriate sealant for the structural or weather seal application, sealant contact with incompatible materials, damage to adjacent glass or structural seals from improper cutting or substrate preparation methods, or glass breakage due to damage (e.g. glass edge damage) from mechanical impact or mishandling.
Due to the prevalent challenges and risks associated with field installed SSG, the industry has typically avoided such installations, particularly for large scale applications, without significant measures to control the quality of the installation. ASTM C1401-14, Standard Guide for Structural Sealant Glazing, goes farther to warn that four-sided SSG systems “should not be glazed in a construction-site environment except for breakage replacement or other maintenance considerations.”
the installers shall be trained in the proper installation of dow 795 structural silicone